
One advantage of a shipping container is that it already comes equipped with super-strength and weather-tight roof and walls. Dry wall is often installed to hide the corrugated steel, wiring and foam and give the building a more homelike feel, as well as for added insulation. With the exception of ceramic-based paint, don’t expect other “insulating paints” to provide for much insulation. Hot climates, or at least hot summers, might require reflective paint on the outside of the building. Simply applying a closed-cell foam layer to the inside and outside walls of the building will work wonders for insulating against most problems of heat, cold and moisture. Plasma cutter (right in photo) – these compress air and electricity to such a degree that they melt the metal as they cut. There are essentially three types of foundations: a traditional concrete block, a crawl space and a basement.Ĭrawl space – these are useful for a certain amount of extra storage when building a full basement isn’t feasible.īasement – when water tables, soil type and bedrock allow, a basement is a good way of making use of more vertical storage and having potential living space.
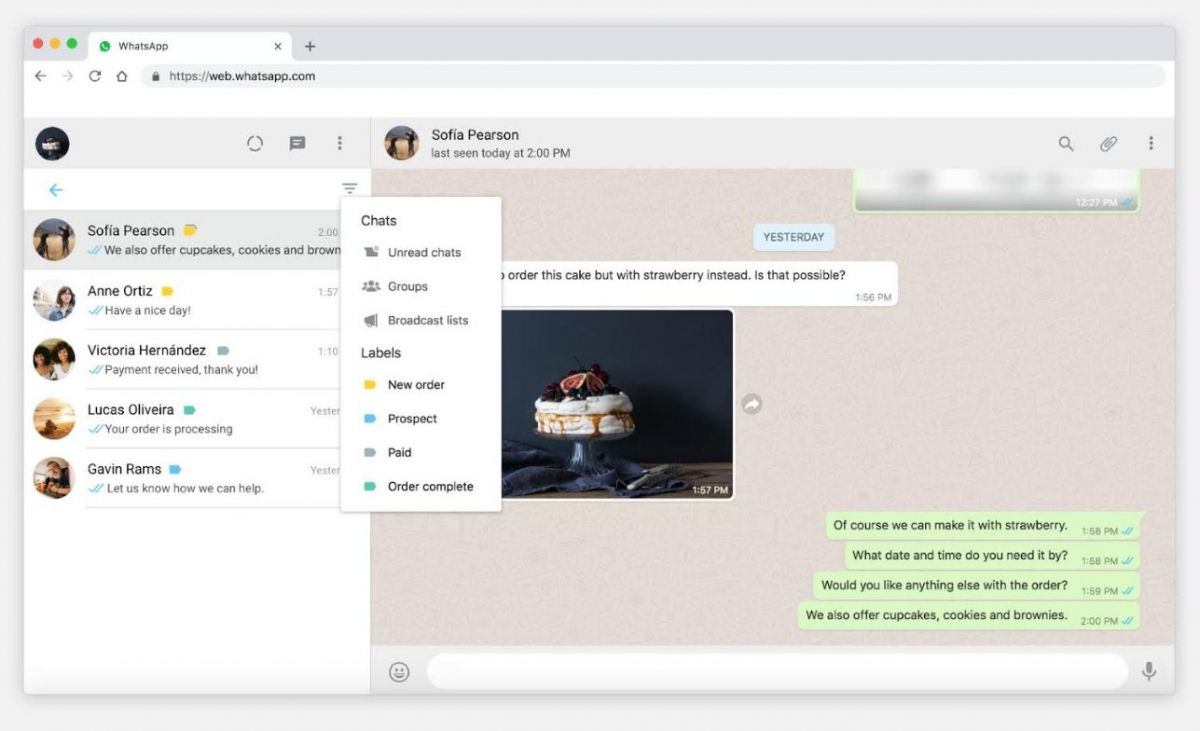
Those who buy a shell and opt to hire a contractor for the rest of the technical work are looking to spend $50 to $150 an hour. There are also a growing number of manufacturers that are designing prefabricated shipping container houses for $15,000 and up. ISBUs are made of 100 percent Corten Steel, and there are a range of different sizes for them. They can withstand practically any extreme weather, such as hurricanes, tornadoes and earthquakes. Since they are originally built for transport, they can be easily moved when they need to be. Herein is a comprehensive guide for turning shipping containers into homes, their prices and how to buy them.
